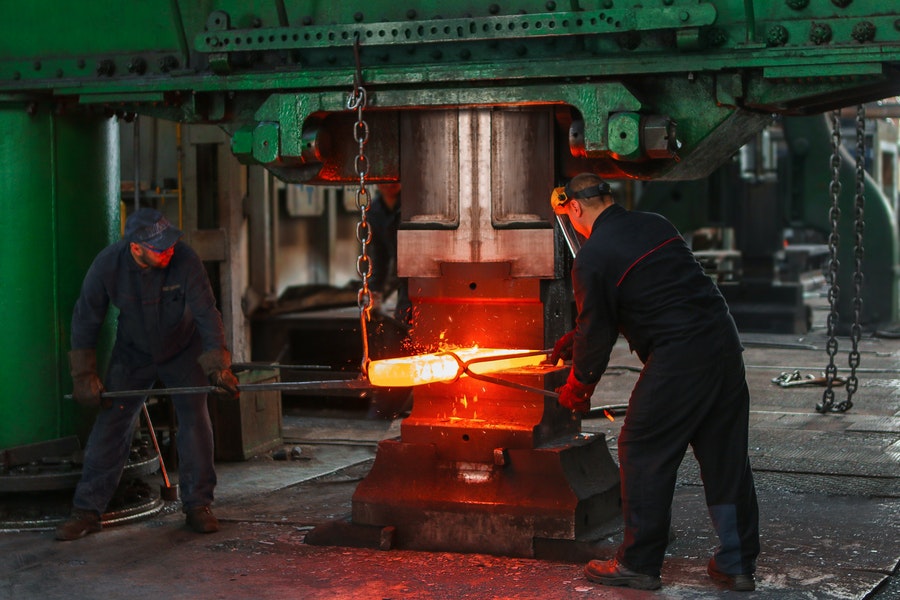
How do you Make Metal Parts?
The earth is not only about layers of rocks and sand we see on its surface. It also contains a variety of valuable minerals that have made our lives far more comfortable than it would be otherwise.
Take the example of metals. Admittedly, we would not have invented many extravagant devices if metal was inaccessible to us. As an experiment, just stroll down your house. The odds are, you will find yourself surrounded by metal appliances right, left, and center.
Remember, metal is initially discovered in a vague form. It is processed through a proper channel to extract the desired cuts and shapes. Though there are endless ways to turn raw metal into polished parts, we have narrowed down the ones that are best in the business. So let’s unveil them without further ado:
Sand casting
The origin of sand casting dates back to 1000BC. Yet, this technique is pretty much alive and kicking till date. In fact, as much as nearly 60 percent of the metal casting is done with the help of sand casting. Its accuracy is particularly admirable when it comes to producing complex figures.
Generally, sand casting implies the usage of naturally-bonded sand because it is less likely to be vulnerable in the face of high temperatures. The spherical grains of sand will not only keep cracking and tearing of mold at a safe distance, but the molten metal will enjoy the sufficient degree of flexibility when the cooling phase kicks in. You may even add clay to further consolidate the boding of particles.
Arguably, the biggest shortcoming of sand casting rests with its low production rate. Because, more often than not, sand molds are demolished to take the metal parts out of it.
Sheet metal
Sheet metal is a unique way to manufacture metal parts. Firstly, the yield strength of a metal is determined, and then the force is applied accordingly. That way, the material is successfully deformed to a level where it can be bent into a variety of shapes and angles in a breeze.
Here are some of the standout benefits of sheet metal fabricating:
- Sheet metal parts are relatively easy to repair. The reason being, you do not have to dismantle their complete structure for marginal alteration.
- The sheet metal process also ensures the durability of metal parts. Because it relies upon numerous kinds of finishing, such as powder-coating, painting, sandblasting, etc. All of them are very handy to save the metal from overexposure of sun, corrosion, and other suchlike nuisances.
CNC machining
CNC machining involves sophisticated usage of technology. Almost everything is monitored and controlled through computers. That is one reason why there is little to no room for human error, and pulling off highly complicated parts is not an uphill task.
Indeed, CNC machining cuts the workforce due to the deployment of heavy machinery. But the overall cost still remains higher compared to the other methods. The only way one can yield the maximum ROI with CNC machining is by mass–producing the metal parts.
Turning
Turning is utilized to create shafts or other rotational parts comprising features such as holes, tapers, threads, and so on. Provided remarkable finishing qualities, it is also regarded as an ideal way to polish portions that were primarily manufactured with the help of other turns and tricks. In simple words, if a part is all dolled up but somewhat falls short of precision, turning can get the job done quite comprehensively.
Die casting
As a manufacturer, you may not always have ample time to complete an order. Because the customers would want you to deliver the parts as early as possible. In such scenarios, die casting is hands down the best alternative. Thousands of metal parts can be formed instantly using only one mold, which makes it an economical option as well. The most time-consuming and challenging step of die casting is to generate formidable molds. As soon as molds are ready, the rest of the process is a cakewalk. Die casting divided into various types, including:
- Low-pressure die casting
- Squeeze die casting
- Semi-solid die casting
- Vacuum die casting
Investment casting
This is also an old-age method that has survived only because of its dead-on-point efficiency. Investment casting is also popularly dubbed as lost wax casting. As far as replicating the internal delicate cuts and angles, this method is second to none. Another upside of investment casting is that you have the flexibility to go for any material such as bronze, aluminum, and stainless steel.
The concluding remarks
We can’t stress enough the importance of metal in our everyday life. But before its availability is ensured to the public for residential, commercial, and other purposes, metal has to undergo a specific manufacturing process. Depending on the demands on customers, companies apply the methods mentioned above to produce metal parts.